Unlock the Secrets of ASA Filament: The Ultimate Game-Changer for Automotive Parts!
As the automotive industry continues to evolve, the demand for advanced materials that enhance performance, durability, and aesthetics is at an all-time high. One such material gaining traction is ASA filament, a type of thermoplastic known for its unique properties that cater specifically to automotive applications. Unlike traditional materials, ASA filament boasts exceptional UV resistance, mechanical strength, and a range of thermal properties, making it a viable option for manufacturers looking to innovate. With the rise of 3D printing technology, the possibilities for using ASA filament in automotive part production are expanding, driving interest from both engineers and manufacturers alike.
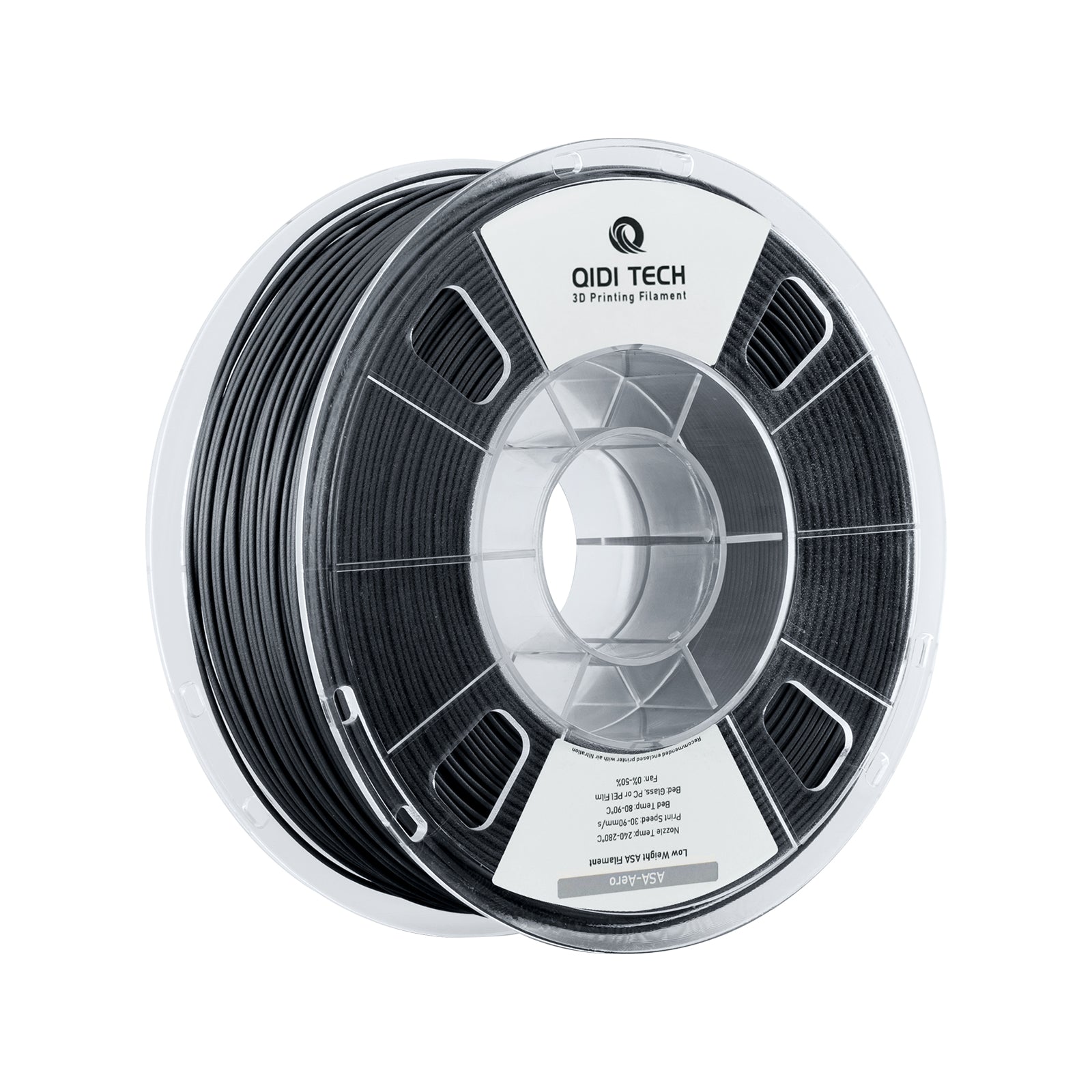
Understanding ASA Filament
ASA filament, short for Acrylonitrile Styrene Acrylate, is a thermoplastic that combines the advantageous properties of acrylonitrile, styrene, and acrylic. This unique blend results in a material that not only exhibits impressive strength and toughness but also maintains its color and structural integrity when exposed to UV light. Unlike ABS (Acrylonitrile Butadiene Styrene), which is often used in automotive applications, ASA is designed to resist weathering, making it particularly suited for outdoor components. The versatility of ASA filament allows it to be used in various manufacturing processes, especially 3D printing, where its ease of use and durability shine. This makes it an ideal choice for creating both functional and aesthetic automotive parts.
Key Properties of ASA Filament
ASA filament stands out in the automotive sector due to its outstanding mechanical properties. It exhibits high tensile strength and impact resistance, which are critical for parts that must endure rigorous conditions. Additionally, ASA has a higher thermal resistance compared to many other thermoplastics, making it suitable for automotive environments where temperature fluctuations can occur. Furthermore, the chemical resistance of ASA filament allows it to withstand exposure to oils, fuels, and other automotive fluids without degrading. This combination of strength, durability, and resistance to environmental factors makes ASA a remarkable choice for automotive applications, ensuring that parts maintain their performance and appearance over time.
Benefits of Using ASA Filament for Automotive Parts
The advantages of using ASA filament in automotive manufacturing are numerous. One of the most significant benefits is its cost-effectiveness compared to traditional manufacturing methods. The ability to 3D print complex geometries reduces waste and allows for rapid prototyping, leading to shorter lead times in product development. Additionally, ASA's lightweight characteristics can contribute to improved fuel efficiency in vehicles, a key consideration for manufacturers focused on sustainability. The ease of post-processing also allows for customization and finishing options that can enhance the visual appeal of automotive parts. Overall, ASA filament not only streamlines production but also elevates the quality of the end product.
Applications of ASA Filament in the Automotive Industry
The applications of ASA filament in the automotive industry are extensive, covering both interior and exterior components. For instance, it is commonly used for creating dashboard components, trims, and bezels that require a balance of aesthetics and durability. Externally, ASA is ideal for parts like mirror housings, body panels, and even custom grilles that need to withstand the elements. Moreover, ASA filament is frequently employed in prototyping, allowing engineers to test designs before final production. This flexibility not only speeds up the design process but also ensures that manufacturers can make adjustments based on real-world performance and feedback. The ability to produce both prototypes and functional end-use parts makes ASA filament a valuable asset in automotive manufacturing.
Future of ASA Filament in Automotive Manufacturing
As we look to the future, the potential for ASA filament in automotive manufacturing appears promising. With ongoing advancements in 3D printing technology, including enhanced printing speeds and improved material formulations, the use of ASA is likely to expand. Additionally, there is a growing interest in sustainable practices within the automotive industry, and ASA’s recyclability and reduced waste during production align well with these goals. Future developments may also include hybrid materials that combine ASA with other polymers to create even more specialized automotive parts. As manufacturers continue to explore innovative solutions, ASA filament will likely play a pivotal role in shaping the future of automotive design and production.
ASI Filament: A Revolutionary Material for Automotive Manufacturing
In summary, ASA filament is emerging as a game-changer in the automotive industry, offering a blend of durability, cost-effectiveness, and versatility that traditional materials often lack. Its unique properties make it suitable for a wide range of applications, from prototyping to final parts production. As manufacturers seek to innovate and meet the growing demands of consumers, embracing ASA filament could lead to significant advancements in automotive design and functionality. The future of automotive manufacturing is bright, and ASA filament is poised to be at the forefront of this exciting evolution.